How
WorksHow
WorksTheBOX® utilizes PuroGen’s proprietary low temperature sterilization and vacuum chamber technologies to create a system capable of safely sterilizing bulk cannabis flower.
With configurable cycles, chamber sizes, accessories and optional features, we can adapt to demanding production environments and processes.
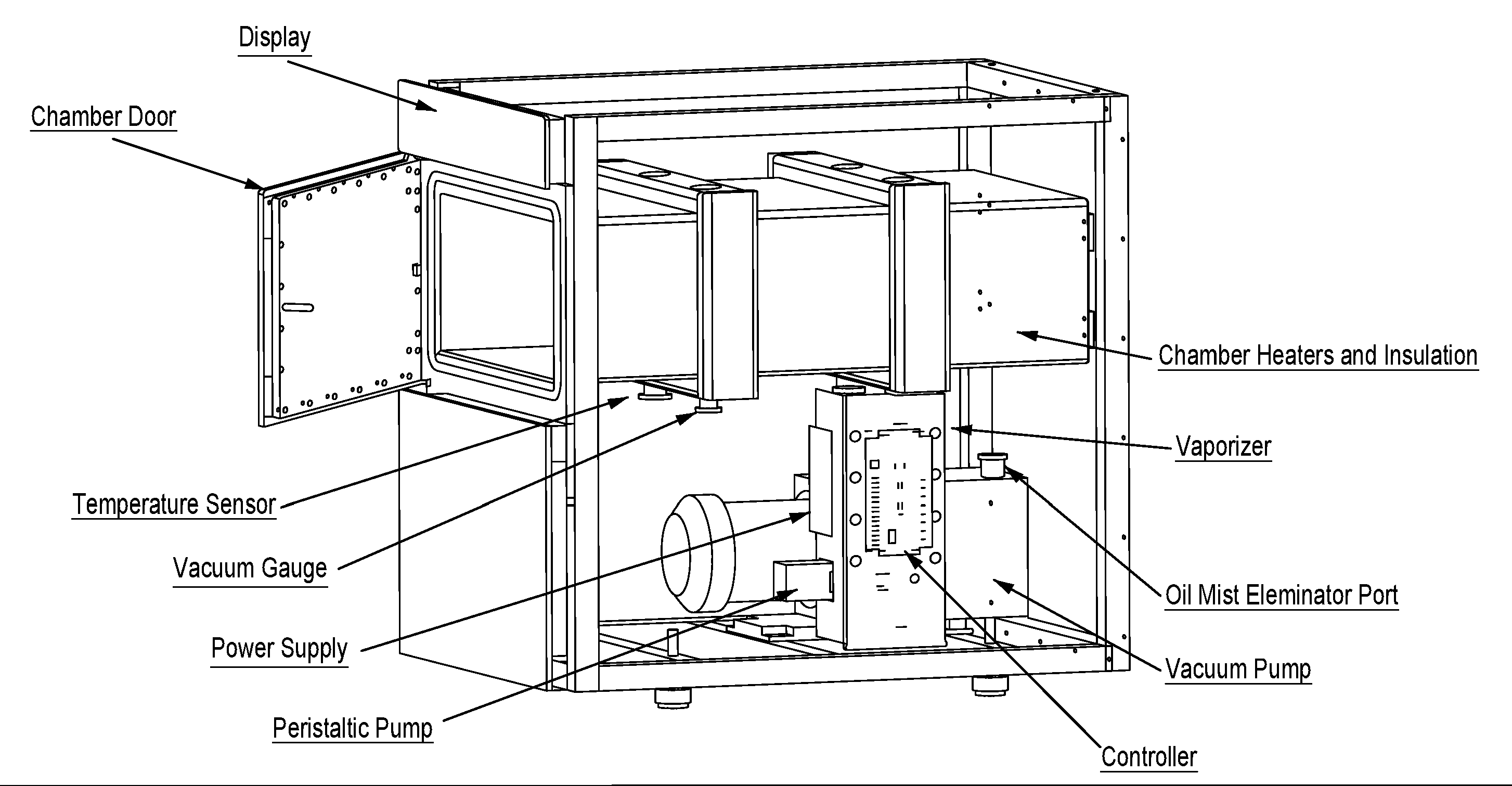
Power Supply
TheBOX uses 110 VAC/ 20 A Single Phase/60 Hz so there is no need to requirement to install additional equipment. The device simply plugs into a standard outlet.
Temperature Sensor
The Temperature Sensor.
Controller
Temperature, humidity, pressure, time and a proprietary low dose Reactive Oxygen vapor are all tightly controlled throughout each cycle phase to ensure efficacy and repeatability. These values can all be pre-programmed through a controller.
Vacuum Chamber
Where packaged organic plant material is placed for purification. Also, where gaseous/aerosolized reagent is introduced and later evacuated during the sterilization process.
The Purification Process
Bio-Decontamination
Reactive Oxygen Sterilant Exposure or Bio-decontamination
Bio-decontamination Phases consists of two distinctive steps: (1) Conditioning Step: where Reactive Oxygen sterilant concentration is brought to the desired level. (2) Exposure Step: where desired sterilant vapor concentration is maintained for a required period of time. Sterilant vapor from a vaporizer is circulated inside chamber. Vaporizer flash vaporizes aqueous hydrogen peroxide solution and disperses it to airstream in a controlled manner. This step is used to increase concentration inside enclosure as quickly as possible to a level slightly below point of saturation. Concentration is gradually increased inside chamber until correct level has been reached.
Exposure
Exposure bio-decontamination step begins when optimal Reactive Oxygen vapor concentration inside the chamber has been reached. Exposure step holds a concentration inside enclosure just under the saturation point until the desired level of bioburden reduction has been achieved. Exact exposure time depends on process type.
Post-Conditioning
During this phase, the load is aerated by circulating air and Reactive Oxygen vapor through the chamber to remove vapor from the load prior to cycle end. Vapor is converted into water and oxygen molecules by using a built-in catalytic converter system. Safe opening of chamber door is ensured by both time limitation (before opening door is possible) and concentration measurement.
An Organic Sterilization Process
Byproducts consist of water and oxygen and therefore is considered an organic sterilization process.
How
EvolvedIn 2005,
Low Temperature Sterilization System was developed as a new and breakthrough technology for the tissue transplant industry that has been since reformulated for cannabis. The process allows manufacturers to sterilize dried cannabis flower on premise, avoiding the time, risk and expense of off-site sterilization services.The commercial cannabis industry deals with age-old threats in the form of biological contamination such as fungus and bacteria. PuroGen made the decision to address these problems by helping professional cannabis growers purify and remediate contaminated products that could potentially pose a serious health risk to patients and consumers, as well as helping avoid potential overwhelming financial losses due to contaminated flower.